Leonidio, a picturesque village in Arcadia, is renowned for its rich tradition in weaving. The famous Tsakonian kilims, with their colorful geometric designs and floral motifs, have adorned the homes of the region for centuries, passing down the unique cultural heritage of the area from generation to generation. Mrs. Metaxia Chandeli, an experienced weaver and connoisseur of this art’s history, guides us through the fascinating journey of weaving in Leonidio. From the introduction of the craft from Asia Minor in the 19th century to contemporary efforts to preserve and evolve it, the history of weaving is inextricably linked with the identity and culture of Tsakonia.
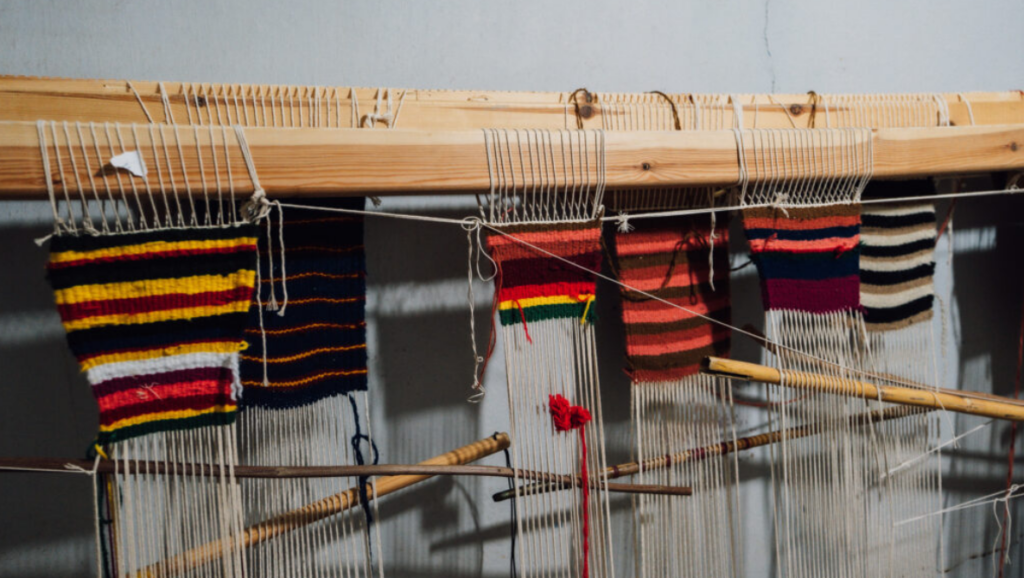
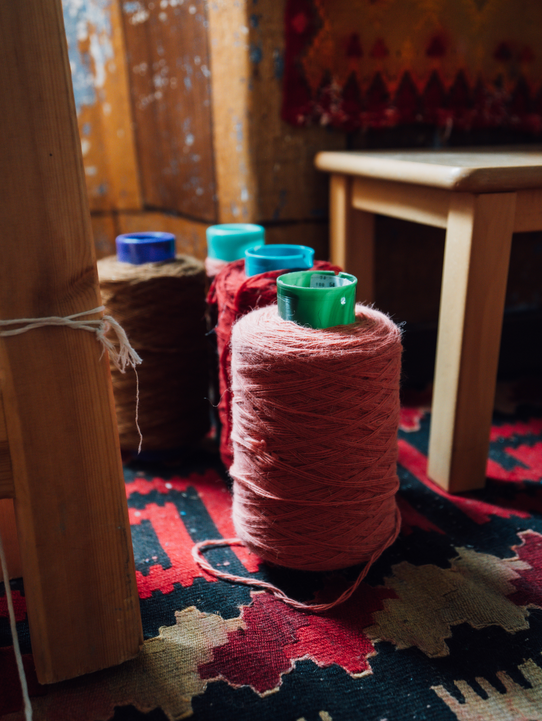
The knowledge shared here is the result of the collective work of teachers of Tsakonian weaving. These include Mrs. Vangeliou Georgitsi, Anna Lysikatou-Koutiva, Metaxia Chandeli, Sophia Kamvysi, and Thomae Korologou. Mrs. Chandeli took the lead in curating our discussion and framing the various topics. The General Secretary, Mrs. Eleni Poutselas, welcomed us at the Tsouchlou Mansion, where, after providing information about the Archive of Tsakonia and the building hosting the exhibition and classes, we had the opportunity to photograph the exhibits and looms.
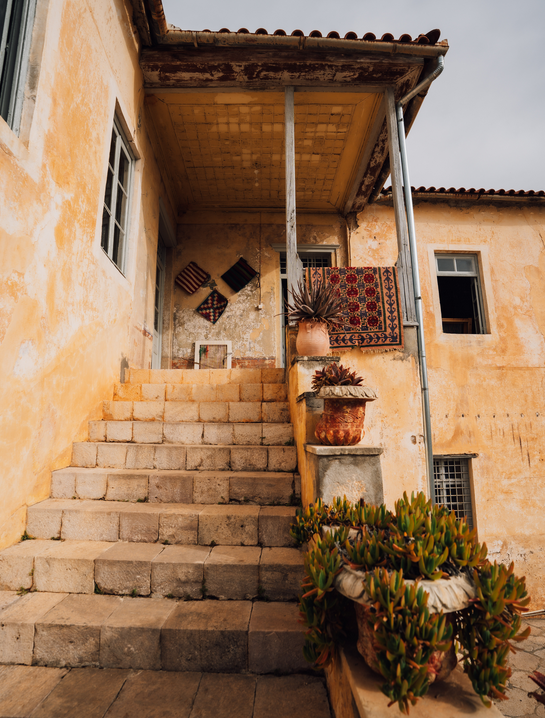
Let us delve into the secrets of this traditional art, the techniques, materials, and symbols behind each kilim. Let’s uncover its significance for the local community and economy and the challenges it faces today in terms of preservation and continuity. Mrs. Chandeli shares her love and passion for weaving, inspiring us to become part of this exciting journey into tradition and art.
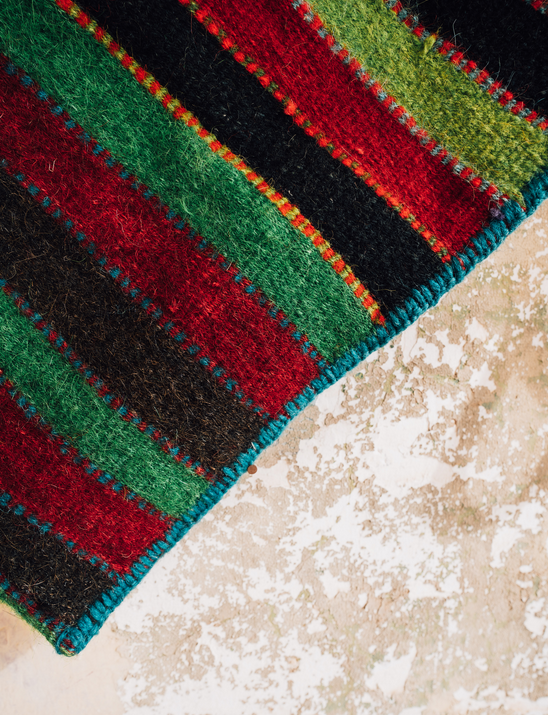
When did the tradition of weaving begin in Leonidio, and how has it evolved over the years?
The art of the Tsakonian vertical loom arrived from Asia Minor around 1870. Polyxeni Dounia came from Aydin, bringing with her the art of kilim weaving, along with designs and colors used in the homes of Greeks in Asia Minor. Polyxeni taught the craft to four students. It took the form of a cottage industry, and over time, a second workshop opened, run by Marigo Merikaki, with students who later set up their own looms at home. Until around 1990, the weaver’s comb never stopped striking the threads and warps. Every home was furnished with this beautiful, warm, and durable kilim. They traveled to nearby villages and even farther as dowries and were also sold in commercial stores in Athens.
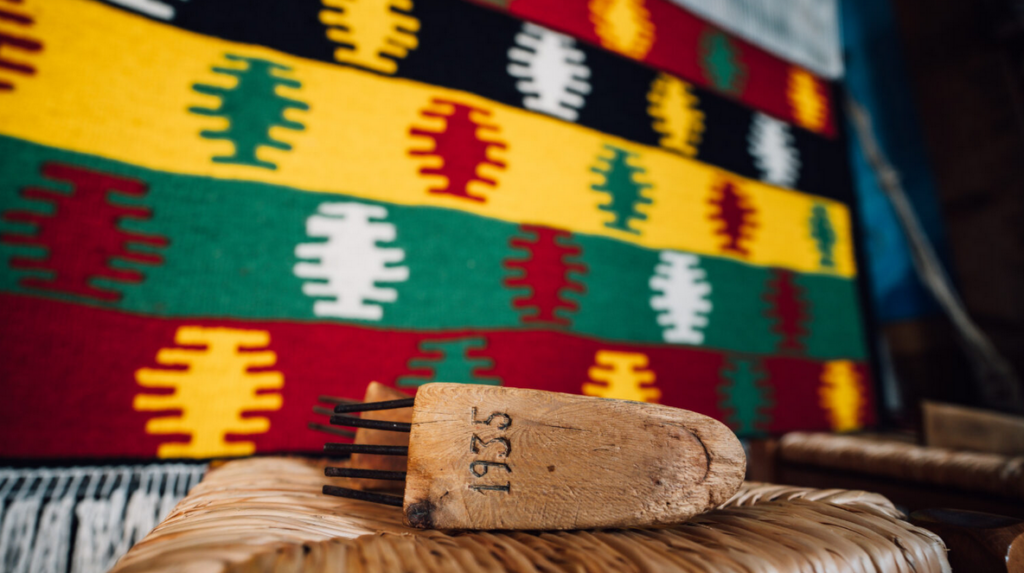
What are the main characteristics of the vertical loom?
The main characteristics of the vertical loom are as follows: Kilims are woven in one piece, giving them the desired dimension without seams, making them durable. They have no pile, so they can be used on both sides. Depending on the size, multiple weavers can work on them simultaneously from both sides.
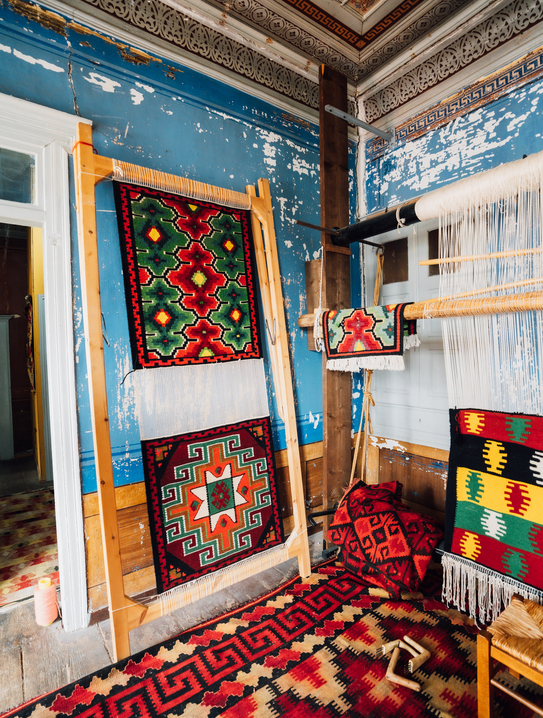
What are the main materials used in weaving in Leonidio?
The material traditionally used for weaving kilims is wool. In the past, during the 1930s, both the warp and the weft were made from sheep’s wool. Later, the warp was made from cotton, while the weft remained woolen. Limited use was also made of goat hair, particularly from billy goats. The back of the animal provided long hair, which was preferred, while the belly produced shorter hair. In May, sheep and goats were shorn. The wool was washed with hot water in large cauldrons. Before about 1975, it was washed in the sea. After it was cleaned, it was washed again with fresh water to remove the salt, then spread out in the shade to dry. It was then teased with fingers to remove any remaining plant debris. This clean and teased wool was carded by passing it between two boards with 5-10 cm metal spikes (similar to nails) to comb it. This soft wool was then spun into yarn using a distaff and spindle.
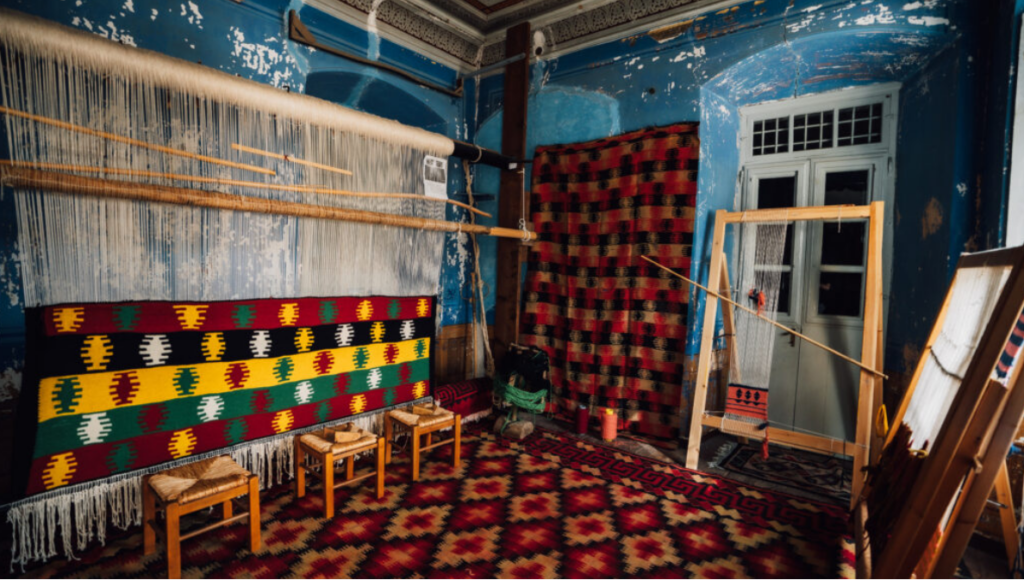
And how did this process continue?
The next step is to make the yarn into skeins and dye it. In the past, yarns were dyed with natural dyes. Walnut bark was used for brown, mulberry leaves for golden hues, onion skins, mallow, nettle, alder, and bedstraw for black, madder for red, and Spanish broom for yellow. Woad was used for shades of blue, while the shellfish murex provided crimson dye. If these plants were unavailable, they were prepared and preserved by boiling them in water or drying them in the sun for later use. Another dyeing method involved using commercial dyes, boiling water in cauldrons, adding dye, alcohol, or potash, and then the wool, which remained in the hot water until it reached the desired color.
How is it done today?
Today, the market offers high-quality, pre-dyed wool ready for weaving. This aids in production and the economy of making kilims. The authenticity, the difference, and the ecological consciousness, the colors that nature provides which chemistry cannot, and the skilled weaver who judges the water temperature by sight all contribute to the uniqueness. The chamomile beige, the muted walnut yellow, are colors no dye can offer.
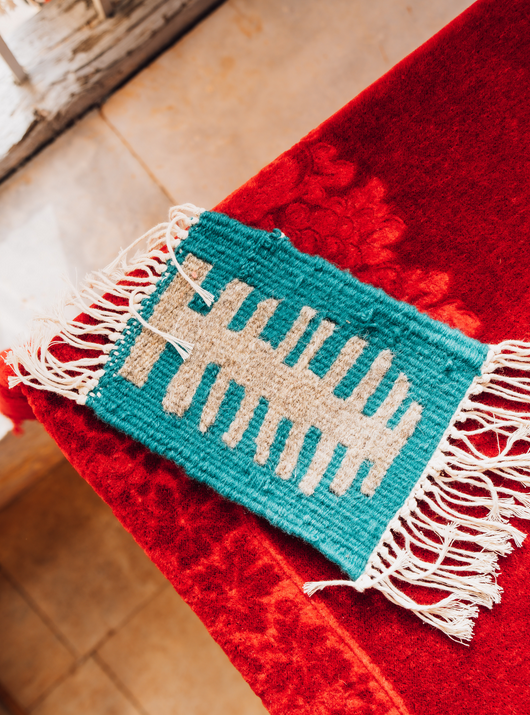
What are the characteristic designs and motifs found in Leonidio’s weavings, and what do they symbolize?
The first designs that came to Leonidio, according to old weavers, included the “kilikas.” The kilim was striped, woven in broad alternating stripes of three colors, typically beige, burgundy, and black. The kilikas was used in less formal rooms. Initial designs were geometric. Later, floral patterns from Balkan countries appeared, brought by merchants from Tsakonia. The “heraki” (little hand) design was the most widespread in various forms, forming strips, small and large diamonds. Every Tsakonian household had such a design. Other popular designs included the disk (hibiscus flower), pansy, American, Tsouchlou (named after a prominent family), cord, tile, shadow, insert, rays, and Byzantine patterns. These designs adorned the living rooms.
The border can be single, double, or even more. It surrounds the main central motif, framing it. The designs are specific: brick, meander, stream, mountain, straight lines, vine, candelabra, etc. Runners: three runners form a “P” shape and are laid out in the bedroom on three sides of the bed. Bags with motifs taken from kilims, with thin or thick stripes. The “pantes” will adorn the wall. All the above designs are inspired by nature (the sun, the pansy), Byzantine motifs, and the imagination and skill of the weavers.
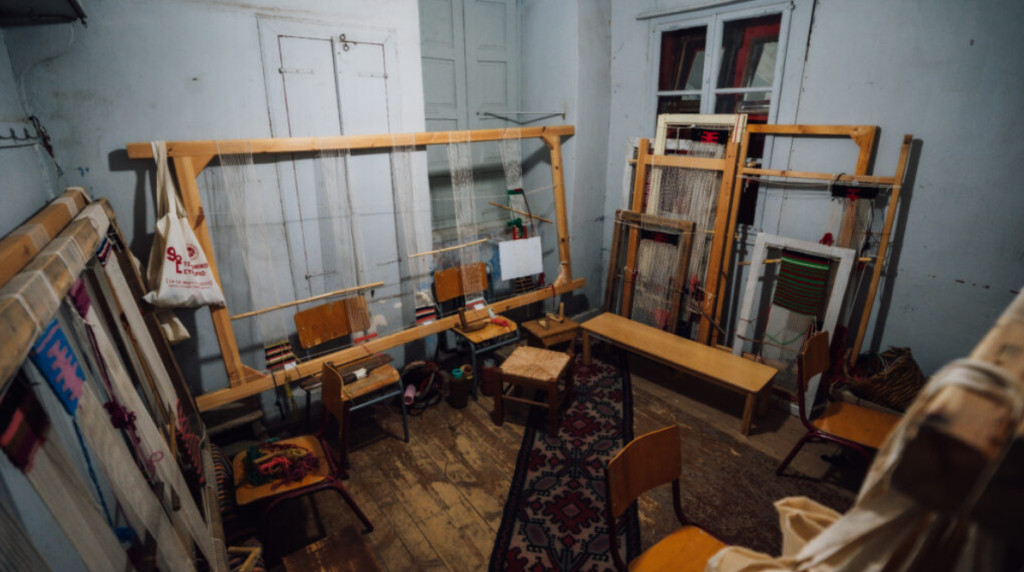
These designs can be found worldwide, from one end of the earth to the other, in various variations. The exchange of designs among weavers creates a communication with the farthest reaches of the earth. I don’t remember any effort from my fellow villagers to explain the motifs. Today, searching the internet, we find explanations for all the motifs: good luck, abundant harvest, happiness, protection from the evil eye, etc.
Can you describe the process of making a traditional woven piece?
We choose the design of the woven piece, gather all the materials (cotton warp and woolen yarn), and start. We set up the loom. It is a process where the warp is placed on the loom. In an outdoor space, we drive two iron stakes into the ground. With the warp, we form figure eights between the two stakes. With specific movements, the weaver takes the warp from the stakes and places it on the loom. Horizontal cylindrical wooden rods will secure the beginning and the end of the warp. The two horizontal beams of the loom are called “palikaria” and are supported by the wall and the floor. This is a very difficult process, as the warps must not get tangled. It requires experience and strength. The loom can reach up to five meters. It needs its own room, large and bright.
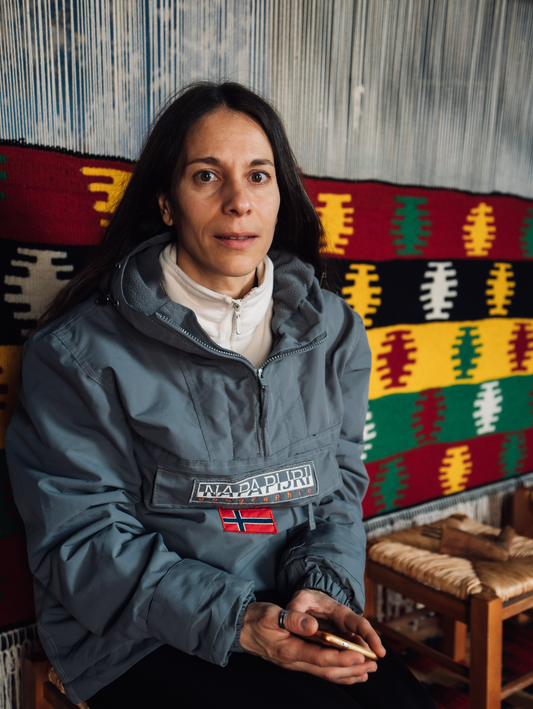
What about smaller woven pieces?
Smaller woven pieces are made on a simple wooden, and less often, metal frame. After tightening the warps, we pass a thin reed-like wood between them and create the cross. One warp is in front of the reed and one behind. The weaver, with her fingers, without a shuttle, passes the yarn through the warps. One is taken, one is left. After forming two or three rows, she hits with force using the comb. The comb is usually a wooden or metal tool. It has a “Γ” shape ending in iron teeth 5-7 cm long. Another tool is the scissors. When the weaving is finished, we cut the warp twenty centimeters from the end and tie it in knots. Then, we make crisscross designs to make it look more beautiful.
What are the biggest challenges faced today by those interested in weaving in Leonidio and preserving this tradition?
The biggest challenge today, for the few who are interested in the craft, is that the art is fading. It has been gradually disappearing since around the 1980s. The reasons are many. We will mention a few. More economical rugs and carpets are available on the market, which are easier to use, lighter, and washable. The Tsakonian kilim is best not washed as it fades. We pass it with vinegar water, which removes dust and makes it shine. The cost of materials is high. Today, a kilogram of yarn costs 25-30 euros. The time-consuming weaving process raises the price. A square meter requires about eight to ten days of work, depending on the design. Unfortunately, a small segment considers the kilim old-fashioned, hence they do not prefer it. Fortunately, there is a small group of women who are trying to save the craft.
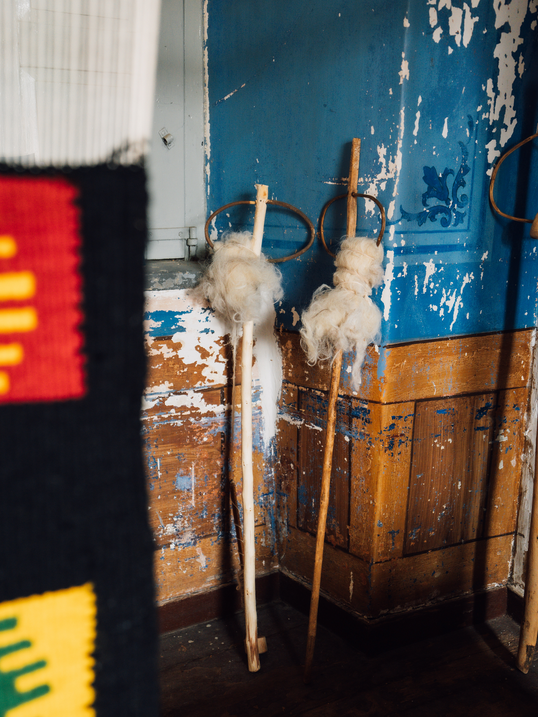
Are there programs or initiatives for promoting and spreading the weaving art of Leonidio to younger generations?
From time to time, initiatives of the Municipality have created weaving sections. They too contributed to the preservation of the art. Today, the Archive of Tsakonia, ally of tradition, culture, and of course weaving, strives to keep weaving alive. In 2016, it established the weaving workshop. Vangelio Georgitsi is the teacher, with Maria Vlami as assistant. Around twenty students started with enthusiasm and zeal to revive, maintain, and develop weaving. Many students of elementary and middle school have learned to weave. Over time, there were losses of students. Despite the reduction in sections over time, several ladies learned to weave and if called upon in the future, they will know how to do it. I would also like to mention that many women know the art, yet do not practice it. The looms are inactive or have been discarded.
Are exhibitions been held?
The Tsakonian Archive organizes at least three exhibitions annually at the Tsouhlo Mansion, where our workshop is also located. This exhibition includes ancient kilims donated by our fellow citizens, as well as kilims we have found in the trash because they have aged. These discarded masterpieces are a lesson for us. We observe the patterns, the colors, etc. There are weavings from new students. They are faithful replicas of older ones and modified versions.
Are classes also taught for visitors?
During the summer, classes are offered for vacationers and visitors in the area. There is interest from all age groups. Visual artists, artists visit, admire, advise us. Some return, and we teach them how to weave. The archive travels with its works to other cities, to various cultural events, exhibitions, and shares, exchanges, and draws inspiration from other places. We have digitized some textiles, old designs. Great comfort for the weaver. Local or non-native educators train their students theoretically and bring them closer to art. Television broadcasts, documentaries, electronic sites visit us often. Tsakonian fabric travels through images and words to the end of the earth.

What is the enduring significance of weaving for the local society and economy of Leonidio?
Tsakonian weaving is part of our culture. It is our identity, closely connected with Tsakonia. It represents our culture. These patterns arrived in our region after the mid-17th century. Previous generations hosted them, weaving them again and again for centuries. They passed them down from generation to generation. It is our duty, our purpose, and our joy to preserve the old, to weave new ones, and to evolve the art, leaving our mark on future generations. The local community does not buy carpets, as every home has at least one kilim and many smaller pieces. Buyers may be Greeks from abroad, mainly Tsakonians and tourists. At this moment, a weaver cannot earn a living.
Can you give us examples of distinctive or emblematic weavings of Leonidio and their history?
Each kilim is unique, special to its owner. It has been sacrificed to acquire it. In middle-class households, it may have been the most expensive possession in the home. If you ask the history of each kilim, the answer will be “it’s my dowry, it’s my grandmother’s dowry.” In homes, at weddings, at funerals, at celebrations, even in summer, the kilim would be laid out. A large kilim of sixty okades was laid out at the services of the church of Agios Konstantinos in Piraeus. Marigo Merikaki, who opened the second consecutive crafts production of kilims, participated in exhibitions in Paris and Liege. Her work depicting the Battle of Trafalgar caused admiration in an exhibition in Athens. The downfall of Admiral Nelson was like a painting. The initials of the owner are written on the kilims.
What are the prospects for the future of weaving in Leonidio and what can be done for its further development and promotion?
The future of weaving in Leonidio is bleak. Weavers do not practice the profession because there is no demand in the Greek market. Schools for learning the art and promoting weavings should support our region.
Ask me anything
Explore related questions